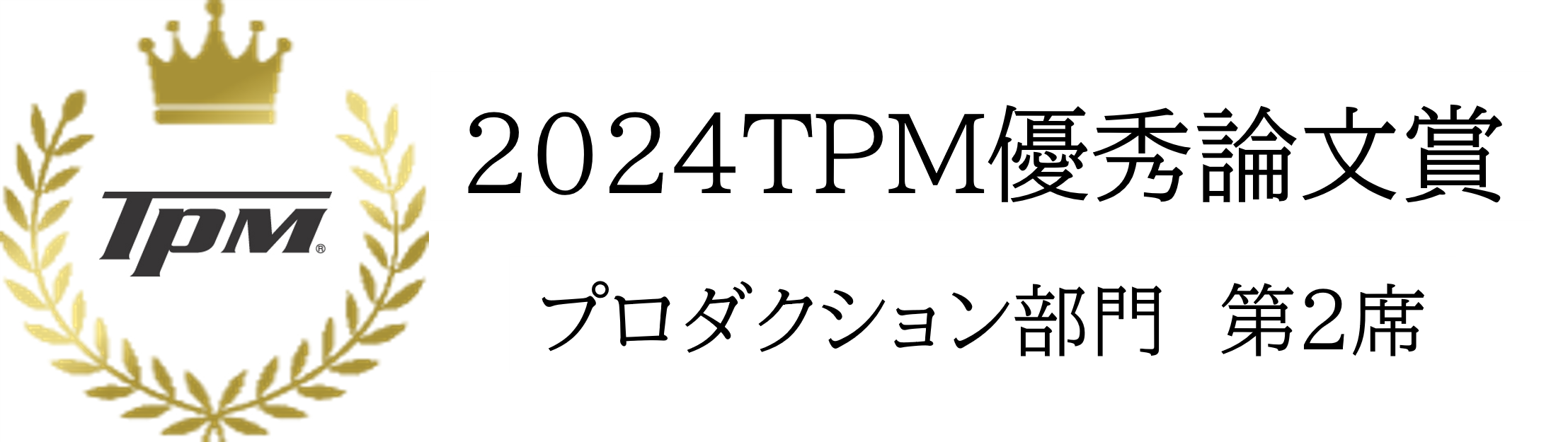
執筆者
ヤマハ発動機株式会社
生産本部製造技術統括部 PF車体技術部新機種グループ
阿部 正和
論文要旨
当社では、主に船外機に使用される外装骨格部品について、射出成形により熱可塑性樹脂で製作している。外装骨格部品では、他部品との締結に際して外装骨格部品に埋め込まれた真鍮製のナットを使用している。真鍮製ナットは自動機に搭載された誘導加熱装置により加熱され、熱可塑樹脂製の外装骨格部品に圧入されるが、消耗品の交換頻度や生産性に課題があった。加えて、圧入工程で使用する自動機は、サイクルタイムが射出成形工程より長く、射出成形工程と圧入工程を同期生産するにあたり射出成形工程のサイクルタイムを圧入工程のサイクルタイムに合わせて伸ばす必要があり、製品サイクルタイム短縮の阻害要因になっていた。
本稿では、新規に誘導加熱装置搭載の自動機を導入するにあたり、交換頻度の高い消耗品として、圧入時にナットを把持する板バネ状の部品と誘導加熱用のコイルに着目した。これら2つの消耗品について、有限要素法解析結果に基づいた形状変更や冷却方法の変更を行い、消耗品寿命の向上を実現した。
また、生産性及び品質向上を阻害する因子を調査し、新設機の設計にフィードバックすることで、サイクルタイムの短縮及び工程能力の向上を実現したので併せて報告する。
緒言
当社では、主に船外機に使用される外装骨格部品について、射出成形により熱可塑性樹脂で製作している。外装骨格部品では、他部品との組付け時に、水との衝撃による外力や船外機自体の振動に起因する応力に耐えうる必要があり、当社では真鍮製のナットを外装骨格部品に埋め込んで締結構造に供している。
熱可塑性樹脂製品に金属部品を埋め込む方法は、射出成形に用いる金型に埋め込む金属部品を固定したのち金型を締め、溶融した熱可塑性樹脂を射出する型内インサート成形法と、射出成形で作製した製品を成形機から取り出した後に、金属部品を埋め込むアウトサート法の2つに大別される。後者は部品の埋め込み方により、超音波圧入法と誘導加熱圧入法の更に2つに大別される。Fig.1は、それぞれの方法における工程の模式図と、QCD観点でのメリット、デメリットを示したものである。当社では、船外機用樹脂部品の製造工程において、金型内に金属部品を固定する作業時間の削減を目的にアウトサート法を用いており、その中でも超音波圧入時の騒音を避けるべく、誘導加熱圧入法を採用しており、誘導加熱装置を自動機に搭載して運用している。
誘導加熱圧入法をはじめとするアウトサート法では、圧入工程と射出成形工程とを工程分割できる。当社では、圧入工程実施時に次ショットを射出成形工程で作製することで、サイクルタイムを低減し、生産の効率化を図っている。したがって、生産性低下を防ぐには、射出成形工程のロスを刈り取ったうえで、圧入工程のサイクルタイムを射出成形工程のそれより小さくし、圧入工程が射出成形工程に追従できるような工程設計が必要になる。しかしながら、既存機の圧入サイクルタイムは成形工程のそれより長く、圧入工程がネック工程であった。加えて、誘導加熱に使用される銅製のコイル(以下、「コイル」と表記)や被圧入対象の真鍮部品把持に使用しているチタン合金製の板バネ状部品(以下、「先端チップ」と表記)をはじめとする消耗品の寿命が最大で2か月ほどと短いうえに、寿命のばらつきも大きいことからチョコ停や故障の主要原因になっていた。
本稿では、新規で誘導加熱装置搭載の自動機を導入するにあたり、定常作業、非定常作業の双方における生産性向上方法について報告する。既存機について要素作業分析を実施し、ネック工程の削減が可能な仕様を折り込むことで、サイクルタイムの低減に成功した。停止ロス削減の観点から、交換頻度の高い消耗品としてコイルと先端チップに着目した。コイルについて、消耗の要因を高温条件下における酸化銅(Ⅱ)の生成であると判断し、冷却方式を変更することで、高温条件下での酸化速度を低減させ、コイルの交換頻度低減に成功した。先端チップについて、有限要素法解析により、ナット把持を想定した強制変位付与時に曲げ応力が低下する形状を調査し、新設機に使用される先端チップの設計にフィードバックした。これらにより、消耗品寿命向上に成功し、設備の安定稼働に寄与しただけでなく、圧入作業の再現性向上による圧入品質の向上もみられた。
また、生産性及び品質向上を阻害する因子を調査し、新設機の設計にフィードバックすることで、サイクルタイムの短縮及び工程能力の向上を実現したので併せて報告する。
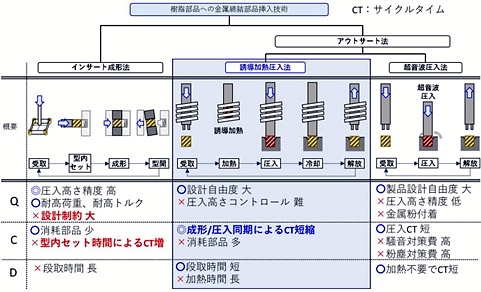
Fig.1 樹脂部品に金属部品を埋め込む各工法におけるメリットとデメリット
既存機における生産性向上阻害因子と対策
Fig.2は既存機の構造と可動軸を模式図的に示したものである。当社では、圧入対象物である船外機の樹脂製骨格部品に対して、上面及び側面の2方向から真鍮製ナットを圧入している。圧入されるナットの個数及び位置は船外機の機種によって異なり、側面からは2か所、上面からは12~17箇所の圧入が行われている。既存機では、対象樹脂部品の成形サイクルタイムが比較的長い(3分程度)ことや多品種生産時の汎用性を鑑み、上面方向、側面方向のそれぞれで誘導加熱装置を2機ずつ、計4機の誘導加熱装置を搭載し、各軸を可動とすることで多品種への対応を可能としている。
ここで、上面からの2つの圧入軸は、それぞれy方向に自由度を有しておらず、y方向の座標調整はワークを載せたパレット搭載軸が担っている。したがって、上面2軸のうち1軸が圧入作業中である場合、もう1軸は圧入実施位置のx座標のみしか合わせることができず、圧入を開始する、すなわちy座標を圧入開始座標に合わせるには、圧入中の1軸の作業完了後、パレット搭載軸が既定のy座標まで動くのを待つ時間(以下、「待ち時間」と表記)が必要であった。

Fig.2 既存機の構造と可動軸の模式図
既存機では、圧入工程のサイクルタイムが射出成形工程のそれより長くなっている機種があり、一部機種において圧入工程ネックになっていたことから、圧入機のサイクルタイム低減が急務であった。既存の圧入機について要素作業分析を行うと、上述した待ち時間がネックになっていることが分かり、仮に待ち時間をゼロにしたことを想定してサイクルタイムを計算すると、最大25sec.程度の短縮代があることが分かった。
また、待ち時間を短縮した際には、誘導加熱によるナットの加熱時間及びエアーブローによる圧入後のナット冷却時間を短縮することで、さらなるサイクルタイムの短縮が可能になることが分かった。以上から、新設機においては、上面圧入用の2軸について、y軸にも自由度を持たせ待ち時間をゼロにすること及び、誘導加熱装置の出力向上による加熱時間の短縮とエアー流量増加による冷却時間の短縮を仕様として折り込み、新設機のサイクルタイム短縮を目指した。
既存機における消耗品寿命調査と新設機採用仕様
生産使用中の定常作業時における生産性向上手法については2項で論じたところであるが、本項では、設備起因によるチョコ停ロスや故障ロス削減の観点から生産性向上に寄与することに着目した。既存機における停止ロスを調査したところ、コイル故障によりナットの加熱ができなくなる故障と、先端チップが繰り返しの圧入により変形し、ナットを把持できなくなる故障の2つが主要因であることが分かった。以下では、これら2つの故障に対して、故障に至る要因を調査し、対策仕様を新設機に折り込むことで、停止ロス削減に努めた。
3.1 加熱用コイル
加熱用コイルは、トランスから印加された高周波交流を受け、連続的に変化する磁場を作ることで、磁場内にあるナットに渦電流を生じさせる役割を担っている。ビオ・サバールの法則より、コイルの作る磁場の大きさはコイルの半径に反比例することから、効率的な誘導加熱のためには、コイルの半径はナットの半径となるべく近しい値であることが望ましいと考えられる。したがって、コイルとナットのクリアランスはなるべく小さく設計されており、コイルは加熱されたナットからの輻射熱を受けやすい環境下におかれている。
コイルは銅のパイプにより作られており、表面には電気的な短絡及びナットからの輻射熱を防ぐことを目的に、ガラス繊維入りの断熱材が巻かれている。既存機のコイルにおいて、ジュール熱及び加熱されたナットからの輻射熱の冷却を目的に、銅パイプの中空部に0.4MPa程度のエアーを流している。
当社では、コイルの使用回数を管理しており、規定回数に達する前にコイルを交換することが管理規定にて定められている。しかし、コイル寿命のばらつきが大きく、規定回数の半分程度の使用回数で故障するものもあり、停止ロスの原因になっていた。Fig.3(a)は故障したコイルの表面写真を、Fig.3(b)は当該コイル黒色部分のみを抽出した写真をそれぞれ示したものである。
故障したコイルでは、表面の断熱材の一部が剥がれ落ちていた。銅のパイプは黒色に変色しており、金属光沢を失っていることが分かった。コイルは銅パイプにより作られていることを鑑みると、コイルを構成する銅がジュール熱及び輻射熱により高温状態におかれ、冷却エアーにより酸素が十分に供給される環境下に曝されたことで、酸化銅(Ⅱ)に変化したことが故障の原因であると考えられた。
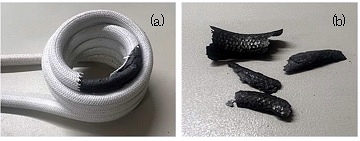
Fig.3 故障後のコイルの様子
また、酸化銅(Ⅱ)が層状に剥離する破壊が見られた。これは、加熱の度に熱サイクルを受けたコイル内で、銅と酸化銅(Ⅱ)の線膨張係数の違いから界面近傍においてせん断方向の負荷が加わり層間剝離に至り、銅の表面が大気環境下に暴露されることを繰り返すことで酸化層が成長していると考えられた。
以上より、コイルの寿命向上には十分な冷却能力の確保が重要なことが示唆されたことから、新設機で採用した加熱装置(UHT-1500;精電舎電子工業株式会社)では、コイル内に精製水を流し、水温を管理することで、十分な冷却能力を担保することを目指した。ナット圧入時は、熱可塑性樹脂を溶融しながら圧入し、規定深さまでの圧入が完了後、エアーブローによりナット及び熱可塑性樹脂を冷却し、樹脂を固化させることで、ナットを埋め込んでいる。したがって、加熱後のナットは樹脂を溶かすだけの十分な熱容量を有している必要があることから、250℃程度まで上昇している必要がある。
季節ごとの気温差に起因するナットの加熱前温度のばらつきを鑑み、ナットを30℃から280℃まで上昇させるのに必要な時間を調査したところ、既存機で7.0sec.、新設機で3.8sec.であることがわかった。Fig.4は既存機と新設機それぞれの加熱装置において、規定秒数(既存機:7.0sec.、新設機:3.8sec.)だけ加熱し、30℃までエアーブローで冷却することを5サイクル繰り返した際のナット表面とコイル表面の温度履歴を示したものである。既存機のコイルでは、誘導加熱中にジュール熱及びナットからの輻射熱で加熱されたコイルが、ナットの冷却終了までに加熱前の温度まで下がりきっていないことがわかる。加えて、4サイクル目以降の加熱において、規定秒数加熱してもナット温度が280℃まで上昇しない現象が見られた。
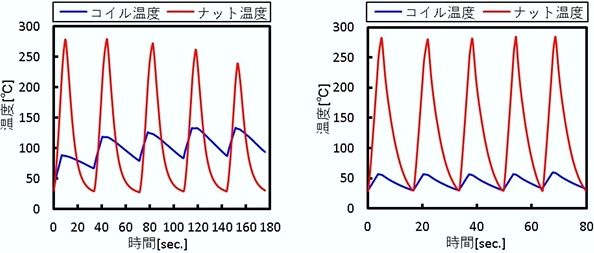
Fig.4 加熱/冷却時のコイル温度とナット温度;(a)既存機の加熱装置(b)新設機の加熱装置
これは、コイルの温度が上昇したことにより、コイルのインダクタンスが上昇し、交流電場の表皮効果により渦電流がナット表面に集中分布しなくなった[1]ことで加熱効率が低下したことが原因であると考えられた。一方で、新設機で採用した加熱装置では、加熱・冷却のサイクル終了後において、コイル温度が概ねサイクル開始前の温度まで低下していることがわかる。すなわち、コイルを水冷化したことで十分な冷却能力を確保でき、既存機よりも高周波数の交流電場でナットの昇温を行うことができる。
以上から、新設機の加熱装置は水冷化による熱容量の拡大により、コイルの長寿命化と昇温時間短縮の双方に寄与できるものであると考えられた。
3.2.先端チップ
先端チップは、ナット供給装置でナットを受け取ってから圧入完了までの間、ナットが落下しないように把持しておく機能を有している。誘導加熱中において、先端チップはナットと共に磁場内におかれる。誘導加熱時、先端チップに渦電流が流れナットの効率的な加熱を妨げることを防ぐため、先端チップは常磁性体で作られることが望ましいと考えられる。また、ナット把持及び解放時に曲げ応力を受けることから、曲げや疲労に対する機械特性に優れる材料であることが望ましい。これらより、当社では、常磁性体であり機械特性に優れる、チタン合金(Ti-6Al-4V)で作られた先端チップを使用している。
既存機で用いていた先端チップでは、ナット脱着時に曲げ応力が繰り返し負荷されることで、先端チップの先端が窄む方向に塑性変形し、ナット把持能力を失いナットが脱落する故障が散見され、それに伴う停止ロスが多いことが問題になっていた。
以上より、新設機導入にあたり、既存機の先端チップ形状について材料力学的観点から検証を行い、より疲労に対する耐久性が高いと考えられる形状に変更することで、先端チップの高寿命化を図った。
Fig.5は、既存機の先端チップの形状を示したものである。先端チップは、圧入機本機とイモネジにより固定されている。ナット把持は、図中板バネ部がナットに挿入され弾性変形することで、反力によりナットを保持する構造となっている。既存機の先端チップにおいて、塑性変形が生じる原因を考える。先端チップに加わる外力は、ナットに挿入された際に与えらえる変位による曲げ応力であると考えられ、板バネ部が片持ち梁構造をしていることから、板バネ部の長さ(Fig.5中のL)を大きくすることで、曲げ応力の最大値を小さくすることができると考えられた。
以下では、既存機の先端チップと、板バネ部長さを既存機比で2.0mm長くした形状の先端チップのそれぞれにおいて、有限要素解析を実施し、曲げ応力の大きさを予測評価した。
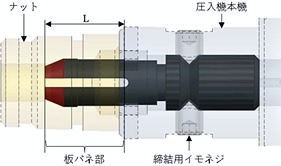
Fig.5 既存機の先端チップ形状
有限要素法解析用モデルとして、板バネ部についてはメッシュサイズ0.05mm以下の三角形要素を、その他の部分においてはメッシュサイズ0.5mm以下の三角形要素を用いてメッシュ作成を行った。
有限要素解析時の境界条件として、締結用イモネジ部は変位、回転共に完全拘束されているものと仮定した。先端部(Fig.5中の赤色面)について、先端チップ外径とナット内径の差分だけ、中心方向に強制変位が与えられているものと仮定した。Fig.6(a)、(b)は上記条件にて大変形を考慮した有限要素解析結果を、ミーゼス応力のコンター図として示したものである。(a)は既存機の先端チップ、(b)は板バネ部の長さを2.0mmだけ延長した先端チップの結果である。
ミーゼス応力分布は双方のコンター図において類似しており、板バネ部根本で最大値をとっていることがわかる。先端チップにかかる最大応力の値は、(a)で497MPa、(b)で320MPaであることがわかり、板バネ部を2.0mm延長することで、解析上最大応力が35.6%低下することがわかった。疲労寿命が104回以上の高サイクル疲労の場合、Ti-6Al-4V合金の疲労強度は、小さいものでは400MPa程度になりうる[2]ことを鑑みれば、既存機の先端チップでは、曲げ応力負荷によりミクロな領域で塑性変形が生じている可能性があることが示唆された。一方で、疲労強度が320MPa程度であるTi-6Al-4V合金についての報告例が見当たらないことから、板バネ部の長さを2.0mmだけ延長し、強制変位付与時にかかるミーゼス応力を320MPaまで低下させることで、先端チップの寿命向上に寄与できる可能性があると考えられた。
以上より、新設機の先端チップでは、板バネ部の長さを2.0mmだけ延長したものを採用することとした。

Fig.6 ミーゼス応力のコンター図;(a)既存機の先端チップ (b)板バネ部寸法+2.0mmの先端チップ
新設機におけるサイクルタイムと工程能力調査結果
前項までで、新設圧入機で採用する仕様について述べた。結局のところ、新設機では、下記の仕様を採用することとした。
1.2つの上面圧入軸において、x,y,z軸についての独立した自由度を持たせ、待ち時間をゼロにする。
2.誘導加熱装置を構成するコイルの冷媒をエアーから水に変更し、十分な冷却容量を確保することでコイル寿命向上を図る。
3.コイルの熱容量拡大に伴い、加熱装置の出力を向上させ、加熱時間を短縮する。
4.圧入後のナット冷却用エアー流量を増加させ、冷却時間を短縮する。
5.先端チップについて、板バネ部の長さを2.0mm拡大し、対疲労特性を改善することで、先端チップの寿命向上を図る。
これら仕様の採用により、チョコ停や設備故障に起因する停止ロスの削減することと、圧入工程のサイクルタイムを短縮することで、成形工程と圧入工程を同期生産することを目指した。
Fig.7は、新設機の構造と可動軸を模式図的に示したものである。2つの上面圧入軸が独立してx-y-z方向に自由度を持つことから、軸同士の衝突を避けるべく、圧入軸間の距離が閾値以下になる場合には電源を遮断するソフトリミットを採用した。また、図中に記載はないが、2つの側面圧入軸についても、汎用性強化のため圧入軸間のピッチを可変できるよう単軸ロボットを搭載した。他軸の圧入待ち時間をゼロにしたこと及び加熱装置の出力を向上し加熱時間を短縮したことにより、圧入工程のサイクルタイムは、短縮効果が最大になる機種で37sec.の短縮を実現した。これにより、圧入工程のサイクルタイムが成形工程のサイクルタイムよりも短くなったことから、成形工程と圧入工程の同期生産が可能となり、生産性向上を達成した。
また、圧入品質の改善も見られた。当社では、圧入品質について、成形品の座面とナット上面との距離(以下、「ナット出代」と表記)を管理項目としている。成形品座面に対してナット上面は凸である必要があり、ナット出代の値は0.5±0.5mmである必要がある。Fig.8は、ある機種におけるナット出代と、工程能力指数を示したものである。
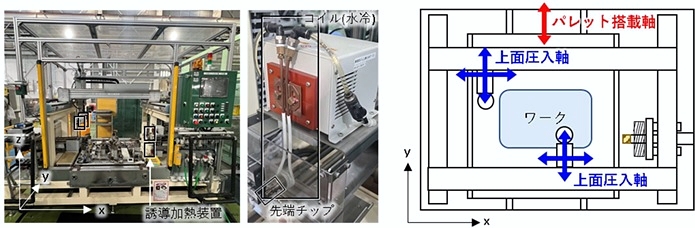
Fig.7 新設機模式図
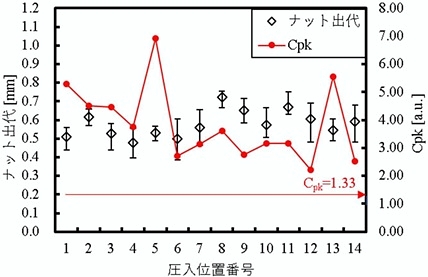
Fig.8 N=50におけるナット出代の平均値と工程能力指数
当該機種は14箇所にナット圧入を実施しており、白抜き黒点で示した値はそれぞれの圧入位置におけるナット出代の平均値(N=50)、エラーバーは出代の上下限値を示している。折れ線はそれぞれの圧入位置における工程能力指数(Cpk)を示している。14箇所の圧入位置において、N=50測定した際のナット出代の最大値は0.72mm、最小値は0.48mmであった。
また、各圧入位置における工程能力指数の最小値は2.21であり、圧入品質について極めてよい再現性が認められた。既存機では、工程能力指数が1.33以下になる圧入位置が存在したことを考慮すると、新設機に採用した仕様は停止ロス削減や生産性向上だけでなく、品質向上にも寄与したと考えられた。
これは、コイルの冷却性能が向上し、すべての位置においてコイルが十分冷却された状態で加熱を開始できることから、加熱後のナット温度のばらつきが低減したことが一因であると考えられた。
新設機における消耗品寿命結果
新設機のコイルにおいて、20,000回(既存機コイルの交換回数)の加熱実施後の劣化状態を観察した(Fig.9(a))。既存機のコイルでは、20,000回の加熱に耐えられず、白色の被覆層が消滅していたのに対し、新設機のコイルでは、被覆部の変色はみられたものの、銅パイプはすべて被覆層に覆われていた。また、被覆層を剥ぎ取ると、銅パイプが赤褐色を示している様子が見られた(Fig.9(b))。銅は室温、大気雰囲気下で容易に酸化し、酸化銅(Ⅰ)を主成分とする酸化被膜を構成する[3]ことを鑑みると、新設機のコイルにおいても銅パイプの表面に酸化被膜が生成しており、酸化の進行を妨げることで、酸化劣化速度の低減に寄与していると考えられた。
本稿執筆現在(2023年10月)、新設機のコイルは無交換で270,000回以上の加熱に使用しているが、被覆層のはがれなど、明らかに劣化と分かる現象は生じていない。現状、新設機のコイルがどの程度の加熱回数まで耐えうるか不明であることから、加熱回数ごとに酸化劣化具合を観察し、故障前に計画的な予防保全を行う目安を定めることが今後の課題である。
新設機の先端チップにおいても、本稿執筆現在1年以上に渡り交換せずに使用できている。先端チップの外径をノギスで測定し、窄み具合を確認したところ、使用開始前と比較して0.03mmの変化がみられた。既存機の先端チップにおいて、ナットを把持する能力が失われる窄み量が0.20mm程度であることを考慮すれば、新設機の先端チップはほとんど変形していないと考えられた。これは、有限要素解析による予測通り、板バネ部を長くしたことにより、ナット把持時に先端チップが受ける曲げ応力を低減でき、疲労特性が向上したことによるものであると考えられた。
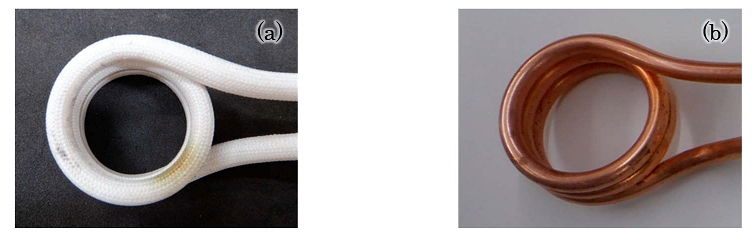
Fig.9 新設機のコイルにおいて、20000回加熱後の観察結果;(a)被覆除去前 (b)被覆除去後
結言
本稿では、主に船外機で使用される熱可塑性樹脂部品の生産工程において、真鍮製ナットを埋め込むのに使用している自動機の消耗品寿命向上方法及びサイクルタイム低減について論じた。既存機で課題となっていた加熱用コイルの寿命の短さについて、コイル冷却時の冷媒をエアーから水に変更することで十分な熱容量を確保し、高寿命化を達成した。これにより、誘導加熱装置の出力を向上しても熱容量上の問題がないことから、加熱時間の短縮が図れ、結果として圧入工程のサイクルタイム短縮にも寄与した。また、ナット把持に使用している先端チップについて、形状を変更しナット把持時に受ける曲げ応力を低減させることで、対疲労特性の向上を達成した。
加えて、既存機におけるネック工程を調査した結果、可動軸を1軸追加することでネック工程をゼロにできることがわかったため、新設機仕様に折り込んだ。前述した加熱時間の短縮と併せて、圧入工程のサイクルタイムを最大で37sec.短縮することができ、射出成形工程との効率的な同期生産が可能になった。
参考文献
[1]DonaldG.Fink、H.WayneBeaty、“Standardhandbookforelectricalengineers.”NewYorkMcGrawHill.、(2000).
[2]皆川邦典、“チタン合金の疲労破壊”、鉄と鋼、第75年第7号(1989)
[3]M.D.SandersonandJ.C.Scully、“RoomTemperatureOxidationofCuandSomeCuAlloys”、CorrosionScience、10pp.55~57(1970)
謝辞
本稿執筆にあたり、精電舎電子工業株式会社の芳賀一嘉氏には、誘導加熱装置におけるスペック資料の教示やコイル形状の提案など、様々なご協力を頂いた。ここに感謝の意を申し上げる。
ヤマハモーターエンジニアリング株式会社の衛藤裕史氏、石田孝之氏には、誘導加熱装置を搭載する自動機の機械設計、電気設計やロボットティーチングの補佐、生産立ち上り後のフォローなど、献身的なお力添えをいただいた。お二人の多大なるご貢献に感謝の意を申し上げる。
新着記事
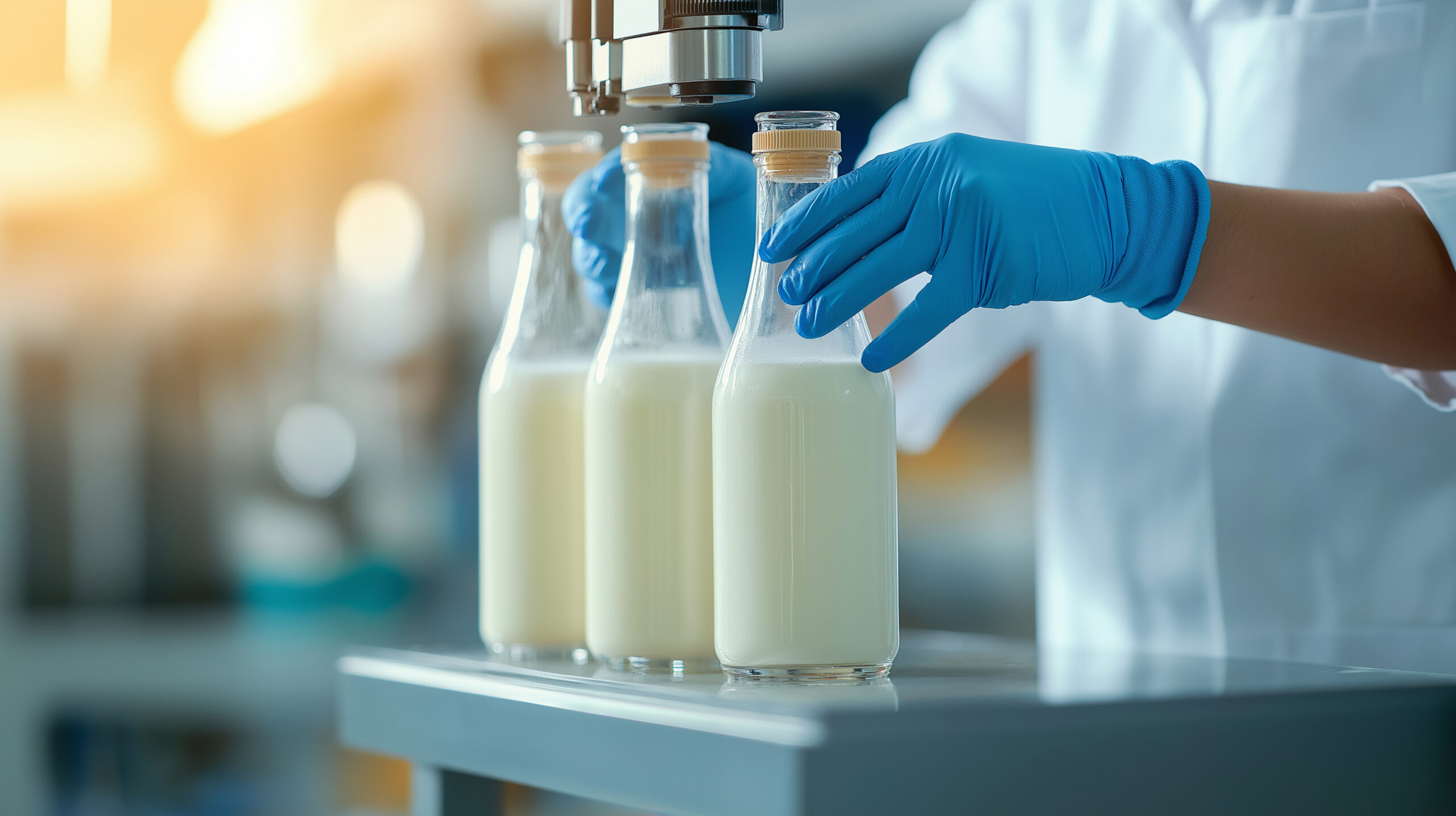
食品工場の進化した自主保全 〜食品安全7ステップ〜②
2025.08.28 無料会員
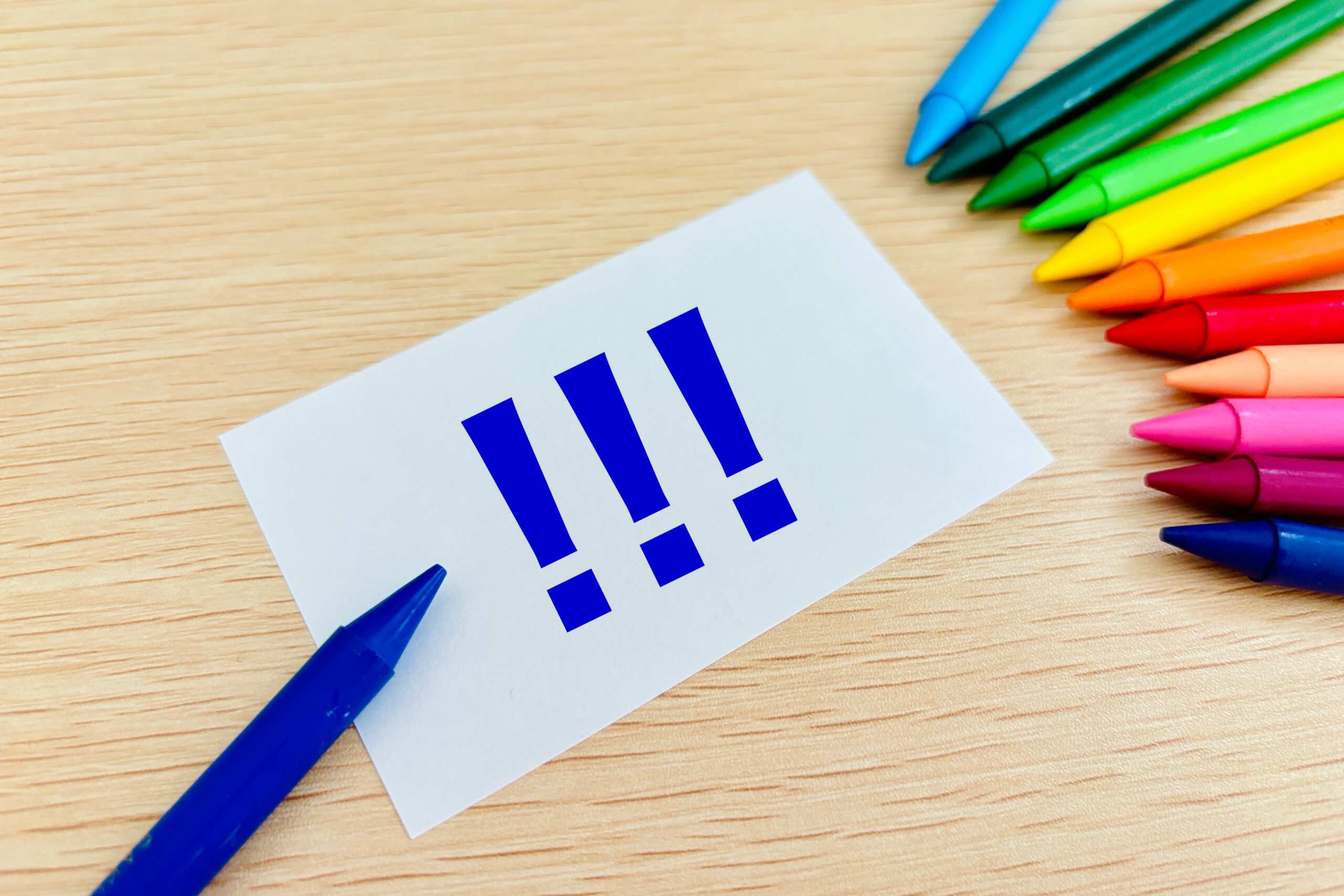
ものづくりの現場力を高める! 自主保全活動のコツ②
2025.08.26 無料会員
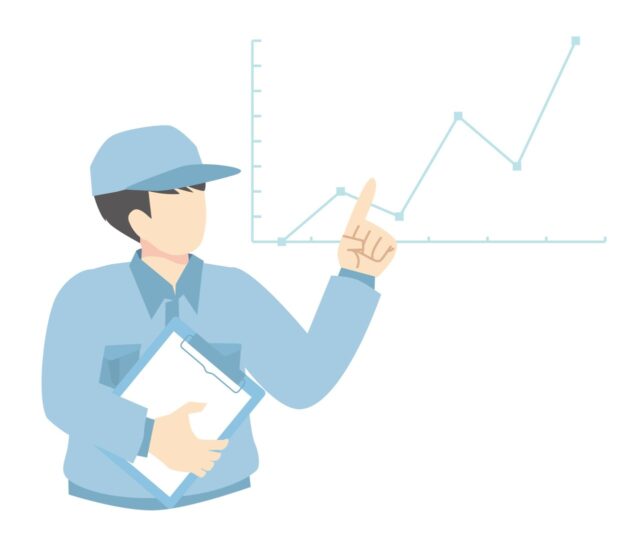
指標でモノづくりを評価しよう! #5 労働生産性
2025.08.19 無料会員
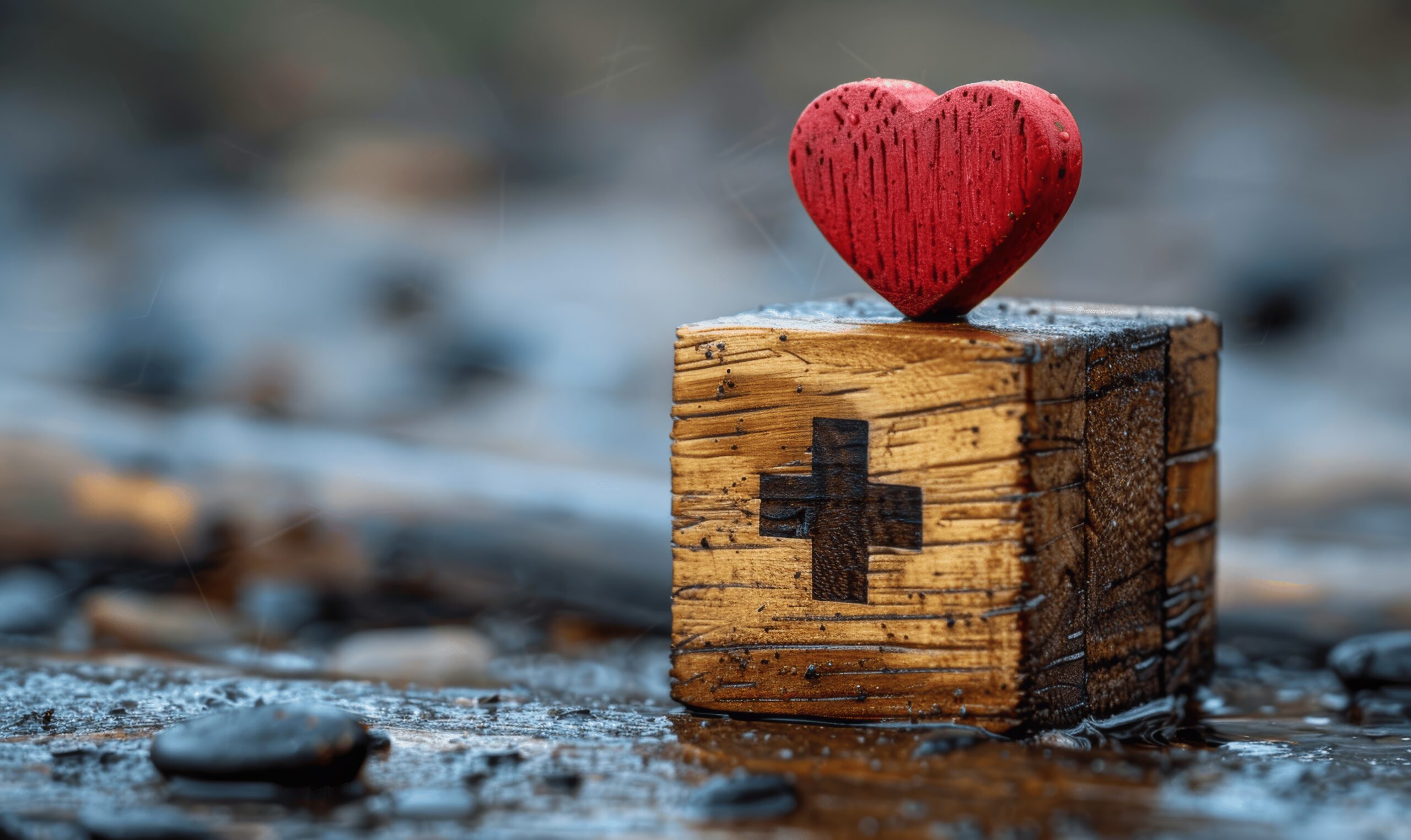
ものづくり屋視点による労働衛生の実践 No.5 安全衛生のリスクアセスメントを再考する その2:共通プラットフォームを活かし有効なマネジメントに
2025.08.18
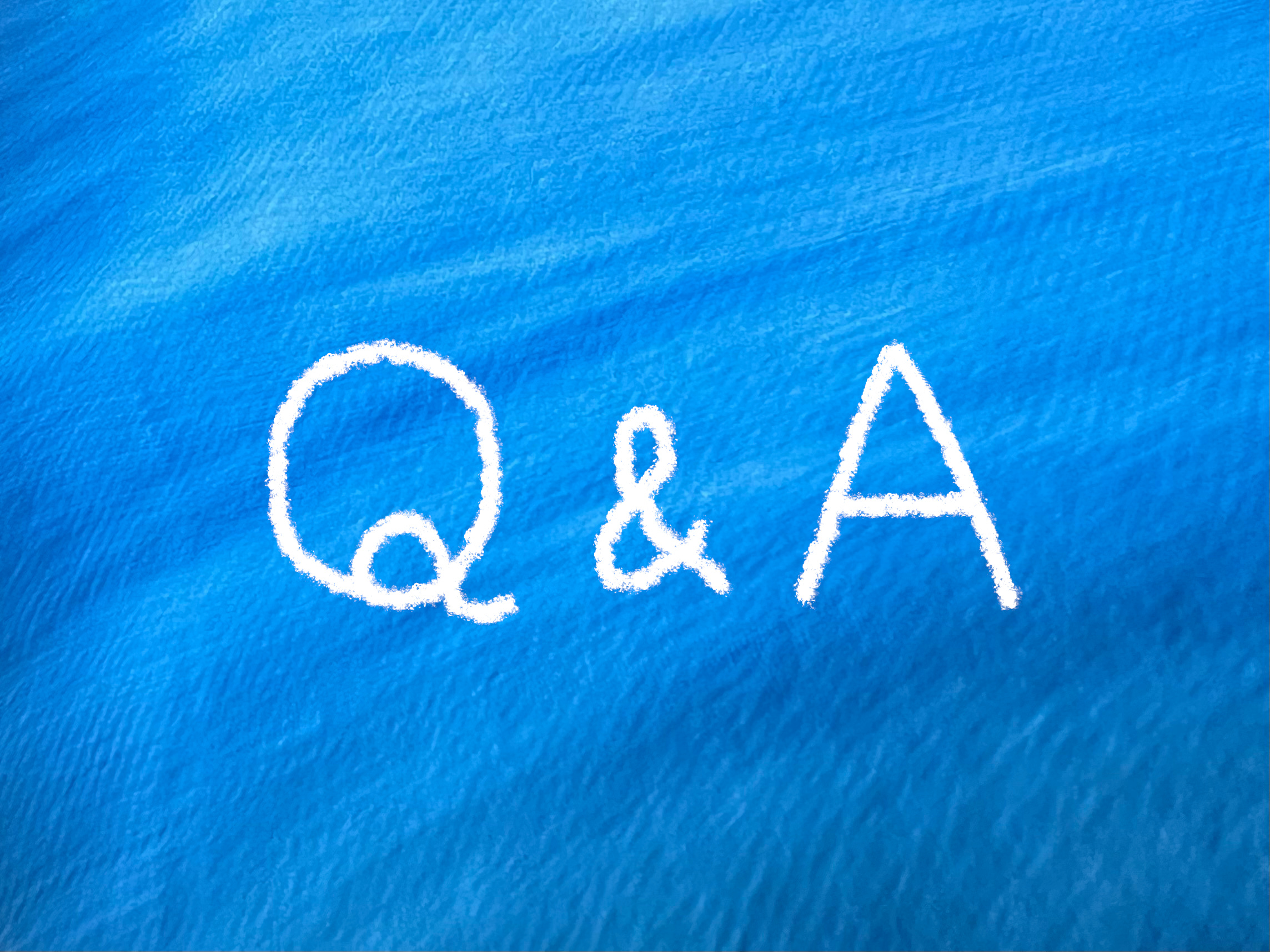
せつびさんとカンリさんの「モノづくり品質の基本のキ」#5 良い仕事をするための基本~その3 QC7つ道具①
2025.08.18
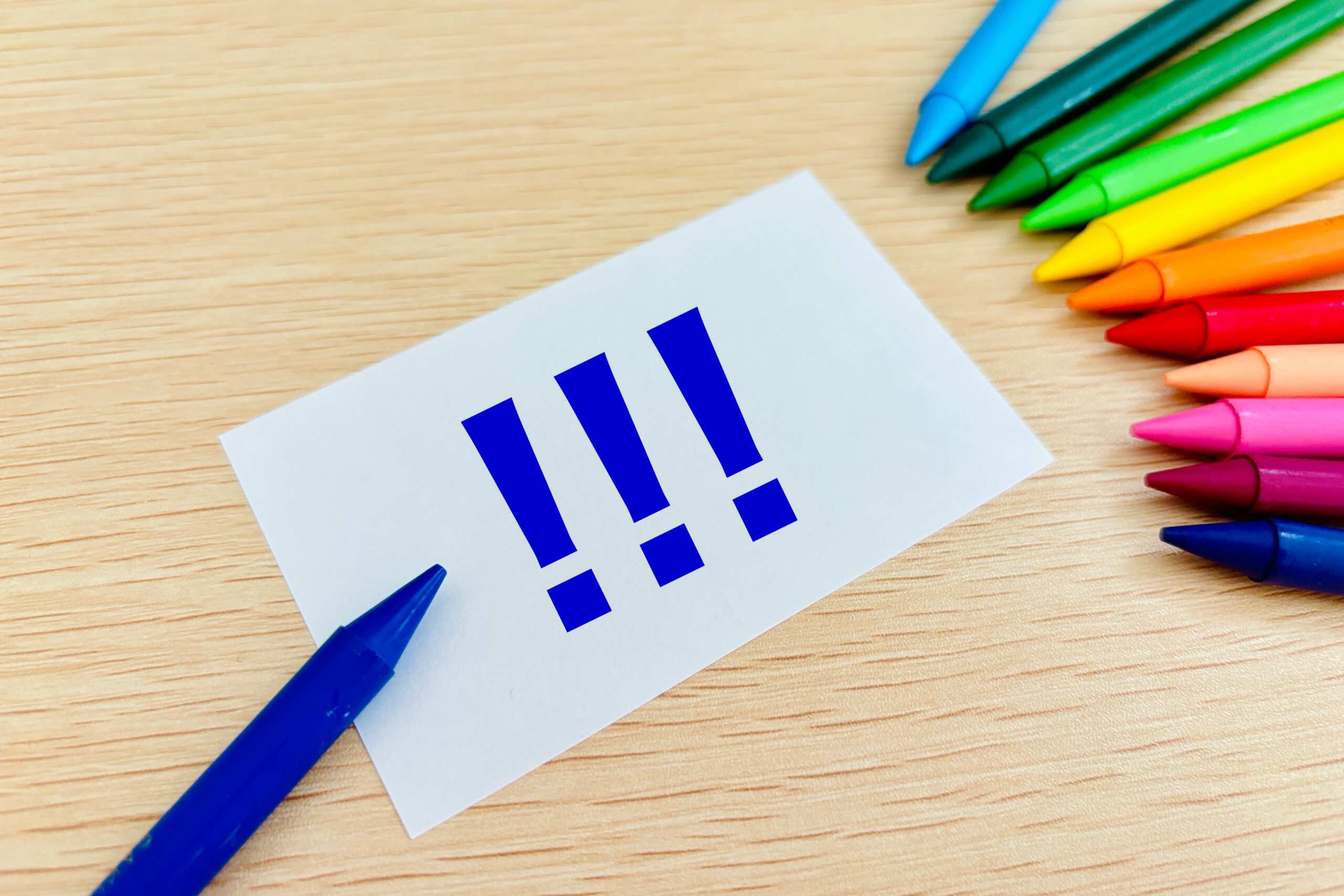
ものづくりの現場力を高める! 自主保全活動のコツ①
2025.07.30 無料会員